An Alliance With Quadra
Project:
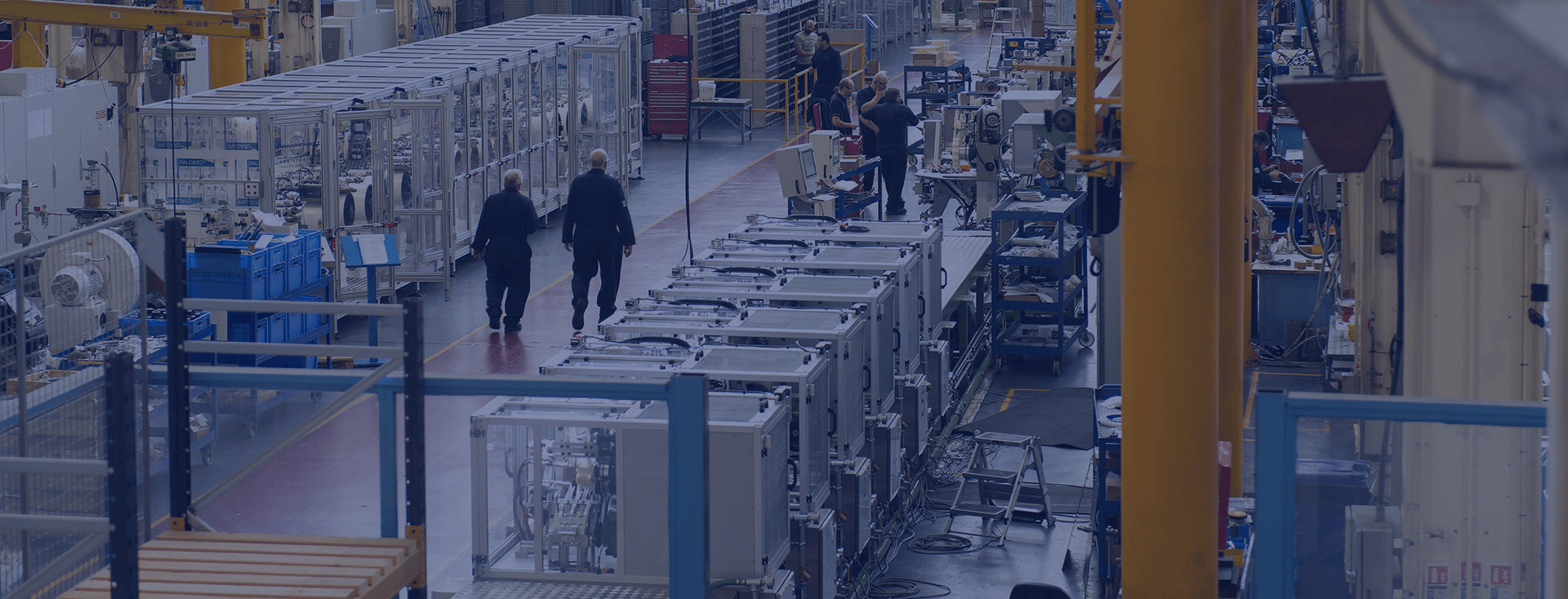
The Client
CarnaudMetalbox Engineering (CMB Engineering) designs, develops and manufactures high-performance metal forming and finishing machinery for the production of beverage, food and aerosol cans. With their commitment to innovation and precision engineering, they continuously strive to break the mold. With CMB Engineering, can manufacturers can keep up with consumer demands, capitalise on market opportunities and ensure production efficiency. They supply precision engineered canmaking machinery to a global market, Canmakers, Trimmers, Beaders, Die Neckers, Bodymakers, Decorators all available from their headquarters in Shipley, UK. They supply solutions to customers around the world and have offices in the UK, America and China.
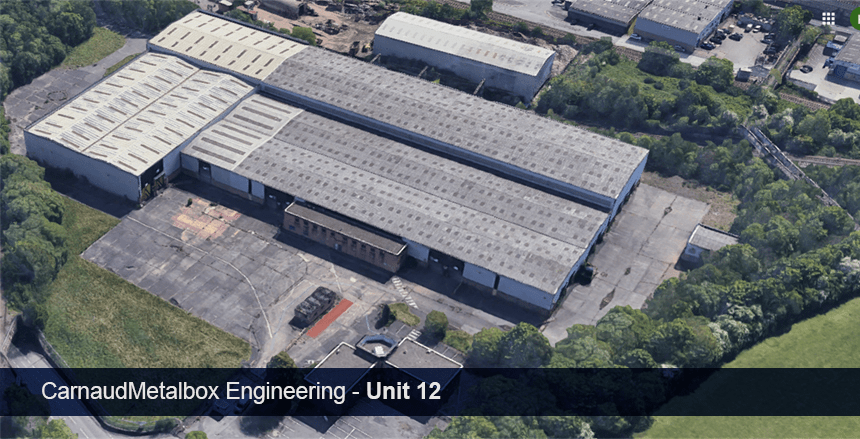
The Project
In 2021 CMB Engineering announced “Unit 12” a new 150,000 ft2 facility in Leeds, West Yorkshire. Significant investment was to be made in the site which was to include brand new AV systems. This project was a collaboration with J-LEC Electrical Contractors who we worked alongside to provide the client a complete solution including:
Key Features
- The Main Boardroom - Large Boardroom Table, Side Cabinet and Touchscreen System
- Two Vice President Offices- Height adjustable work tables, Meeting Desks and Touchscreens
- A Training Room - Lectern and 2 Touchscreens
- A Meeting Room - Meeting Desk and a Touchscreen
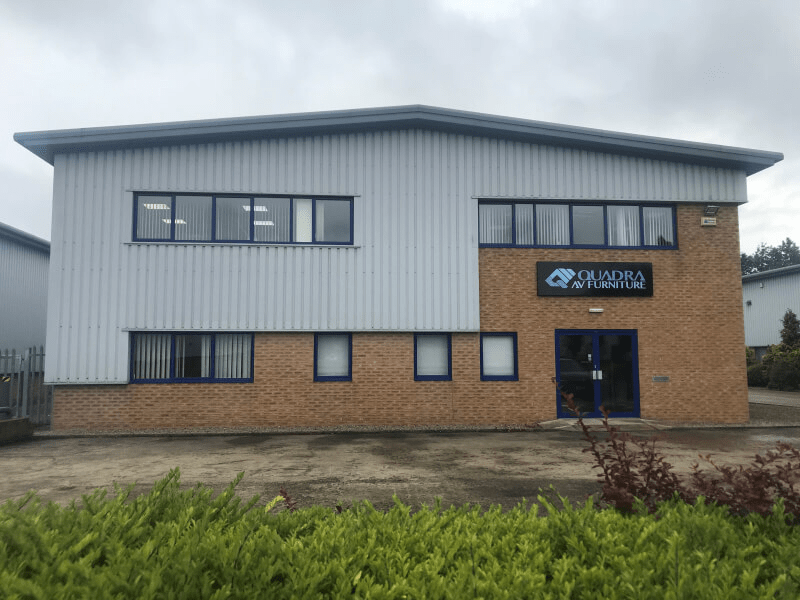
We approached fellow Yorkshire-based company Quadra Audio Visual Furniture (QAVF) to assist on this project.
About Quadra
QAVF furniture has over 25 years experience in the design, build and manufacture of specialist AV Furniture solutions. The company was built on a platform of ongoing investment in production technology and highly skilled craftsmen which enable them to manufacture unrivalled quality bespoke furniture which would be key to the success of this project.
The Process
Ben Crooks, Operations Director at QAVF, visited the new site alongside J-LEC and CMB Engineering whilst it was still under construction. He discussed the clients requirements at length and was able to measure the various rooms that needed fitting out. QAVF's in-house Furniture Designers then drew up the designs & sample renders and the project was quoted for within a couple of weeks of this initial site visit.
Sample Initial Designs
Boardroom Barrel Table:

Height adjustable Desk:
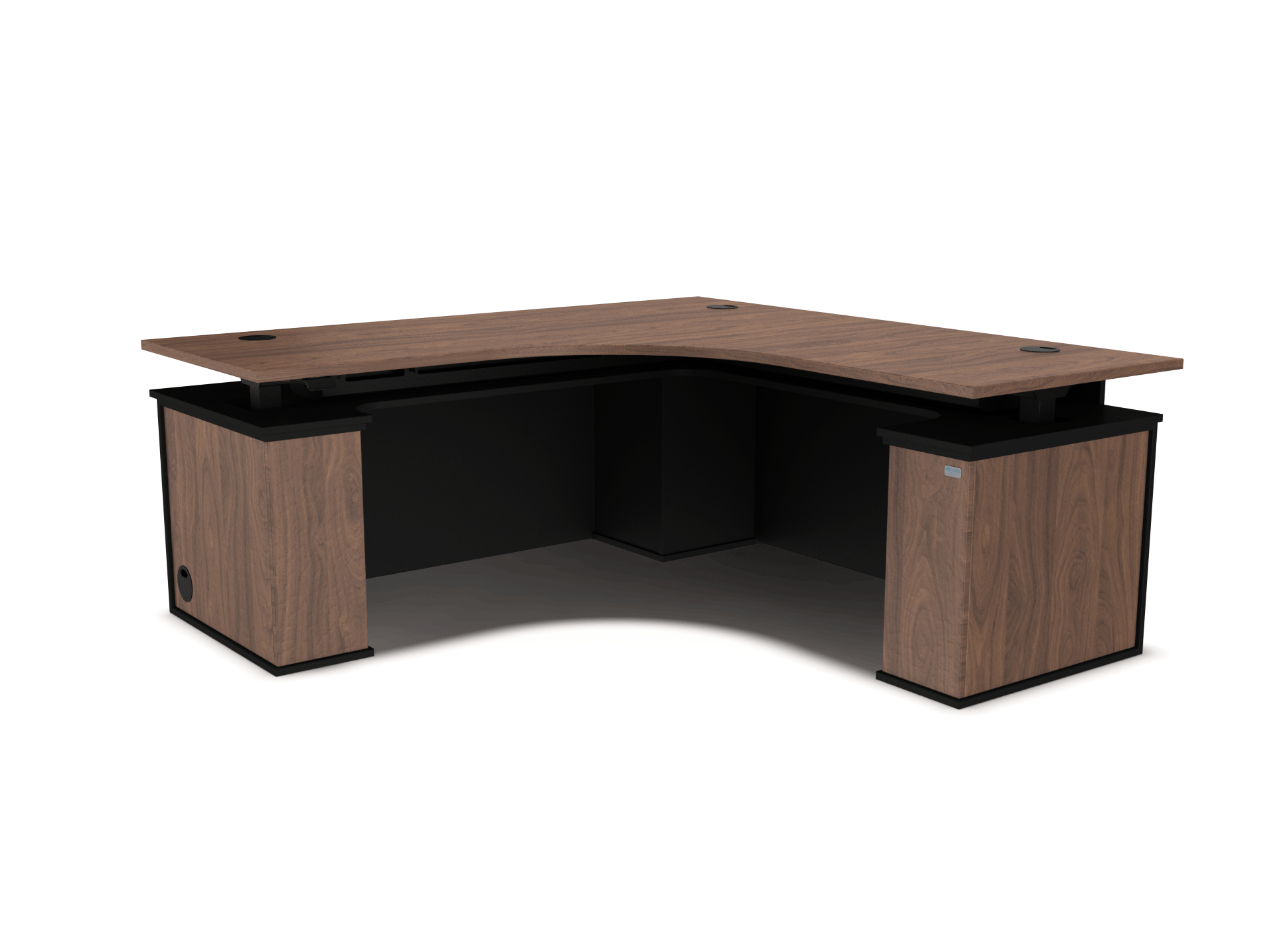
Phase 1: Furniture Installation
Around 4-5 weeks after the initial site visit, QAVF's team of installation engineers installed the furniture over the course of a week and returned to assemble & fit the chairs which were also supplied as part of the project.
Main Boardroom - 20-Seater Barrel Shape Table in a Walnut finish.
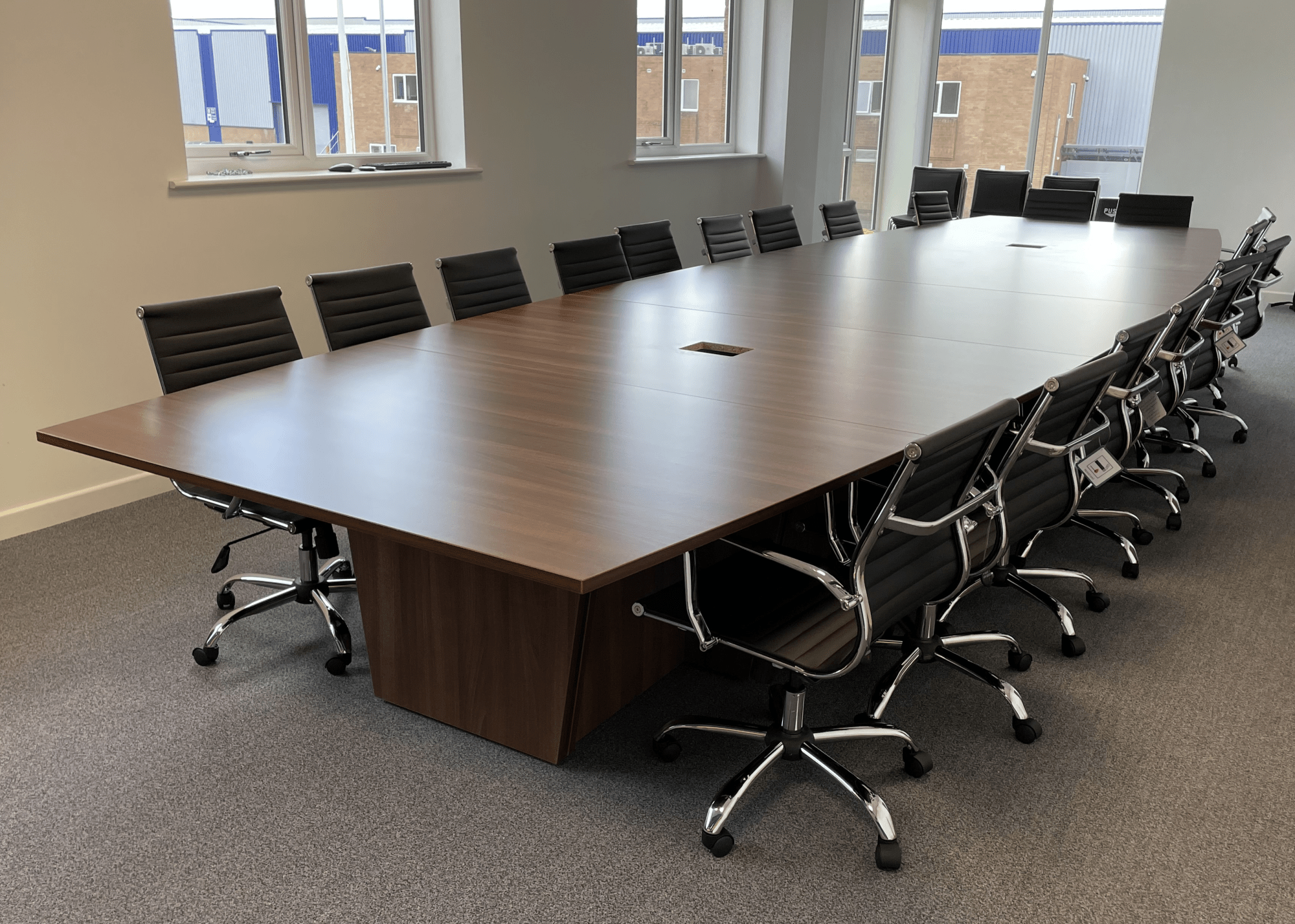
Main Boardroom - Credenza Cabinet (4 compartments) in a Walnut finish.
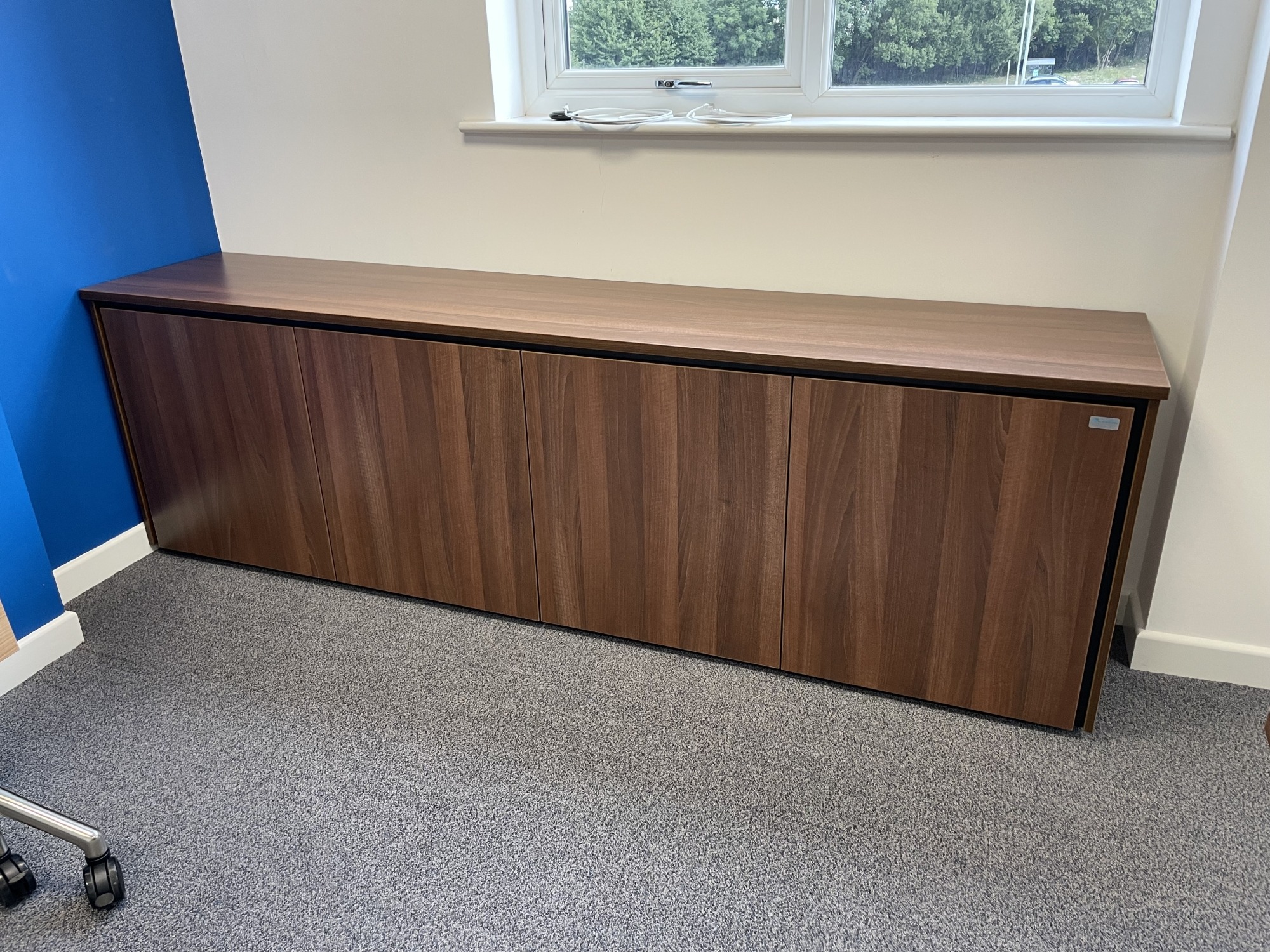
2x Vice Principals Office - Height Adjustable Desk in a Walnut finish (shown standard height):
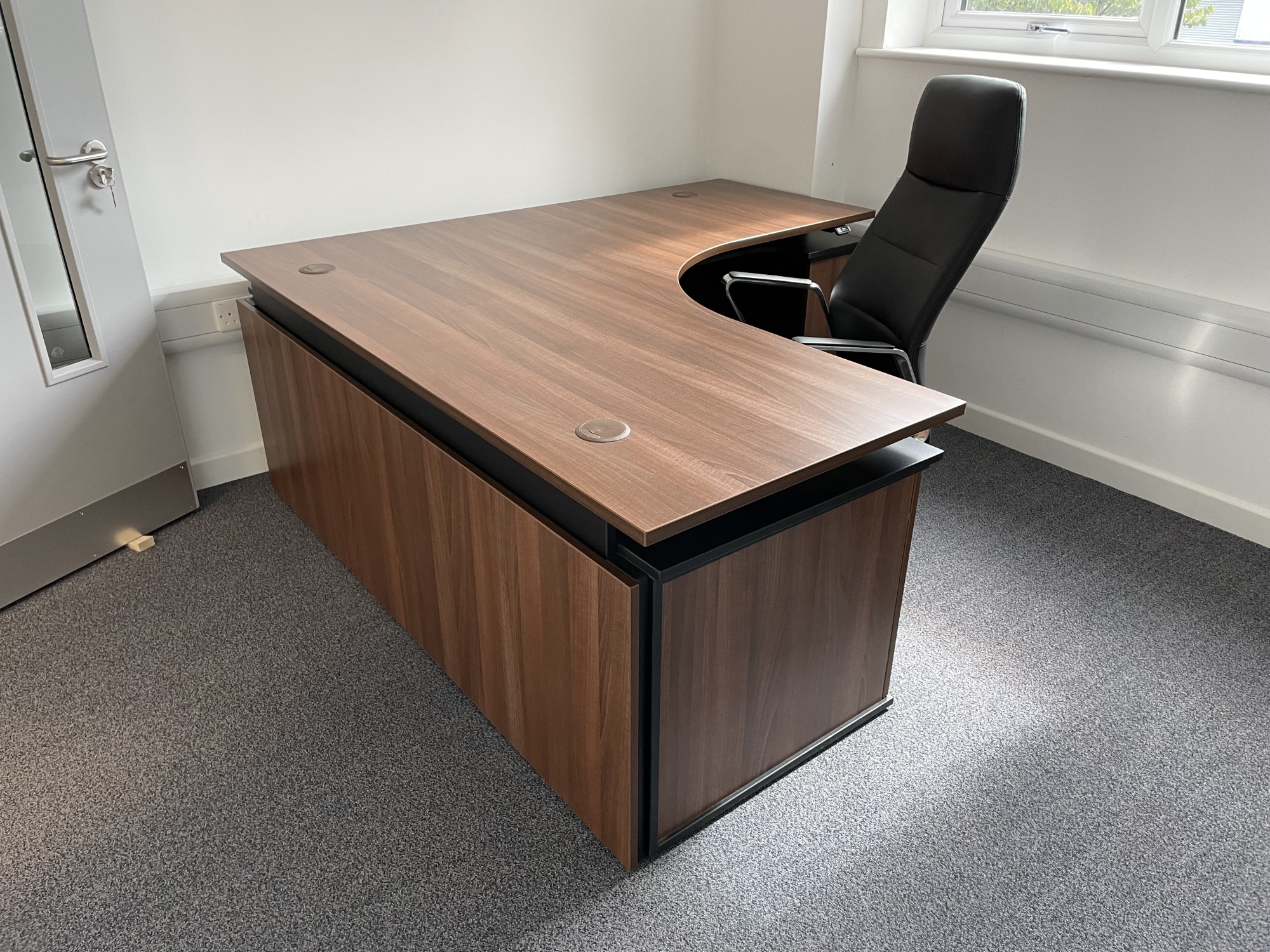
2x Vice Principals Office - Height Adjustable Desk in a Walnut finish (shown raised height):
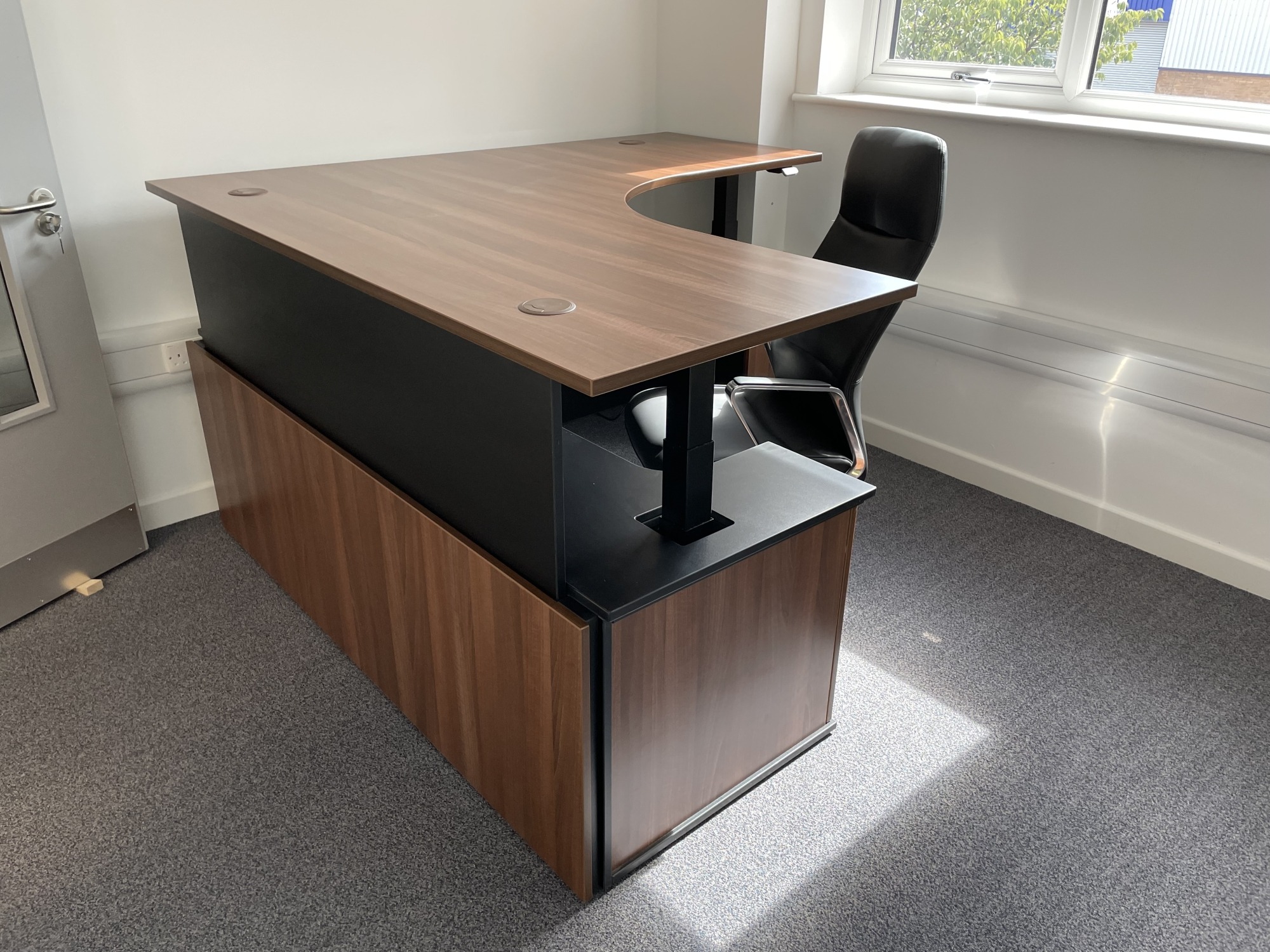
Vice Principals Office - 5-Seater Alliance Collaboration Table in a Walnut finish:
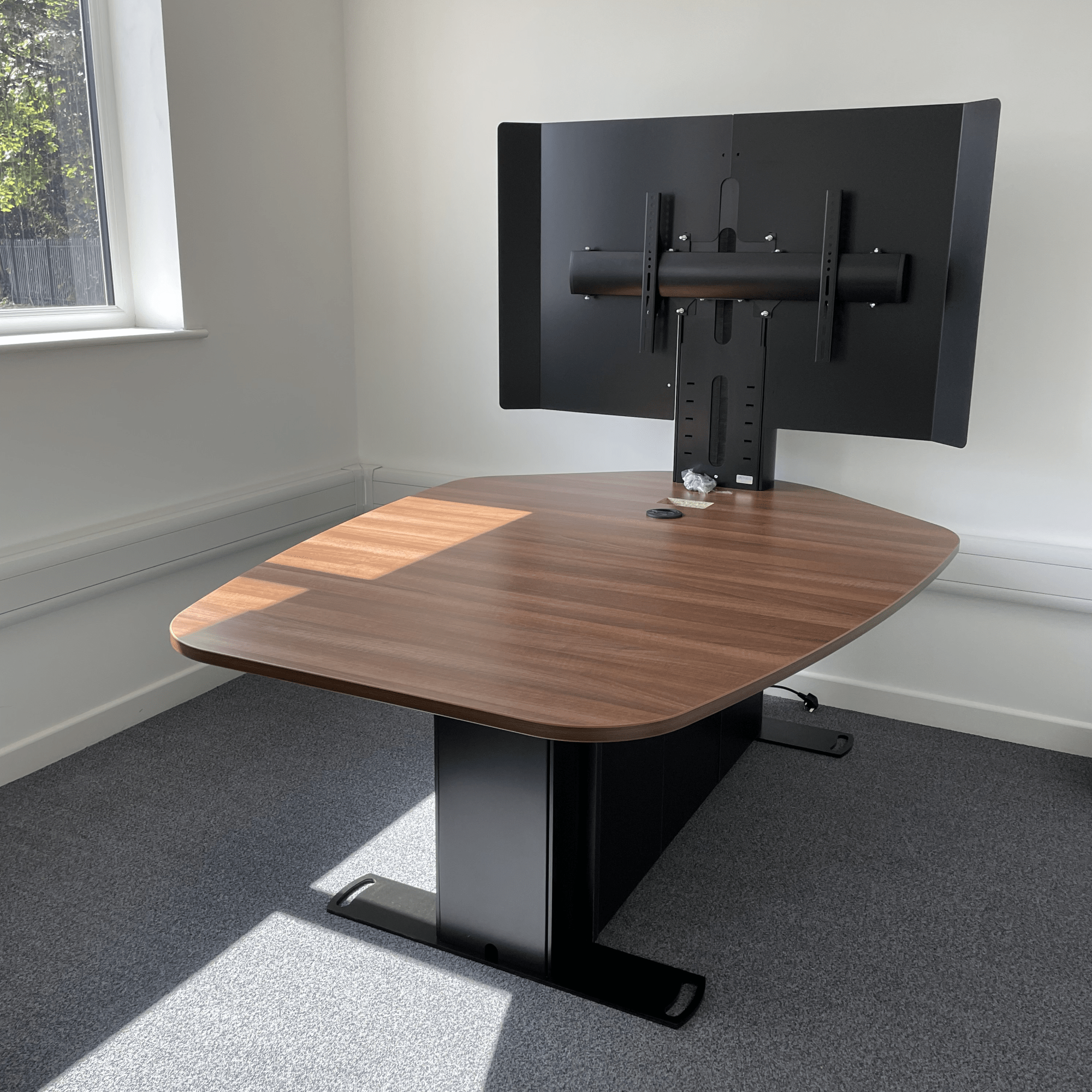
Training Room - Academy Lectern in a Cherry Melamine finish to match folding tables purchased elsewhere:
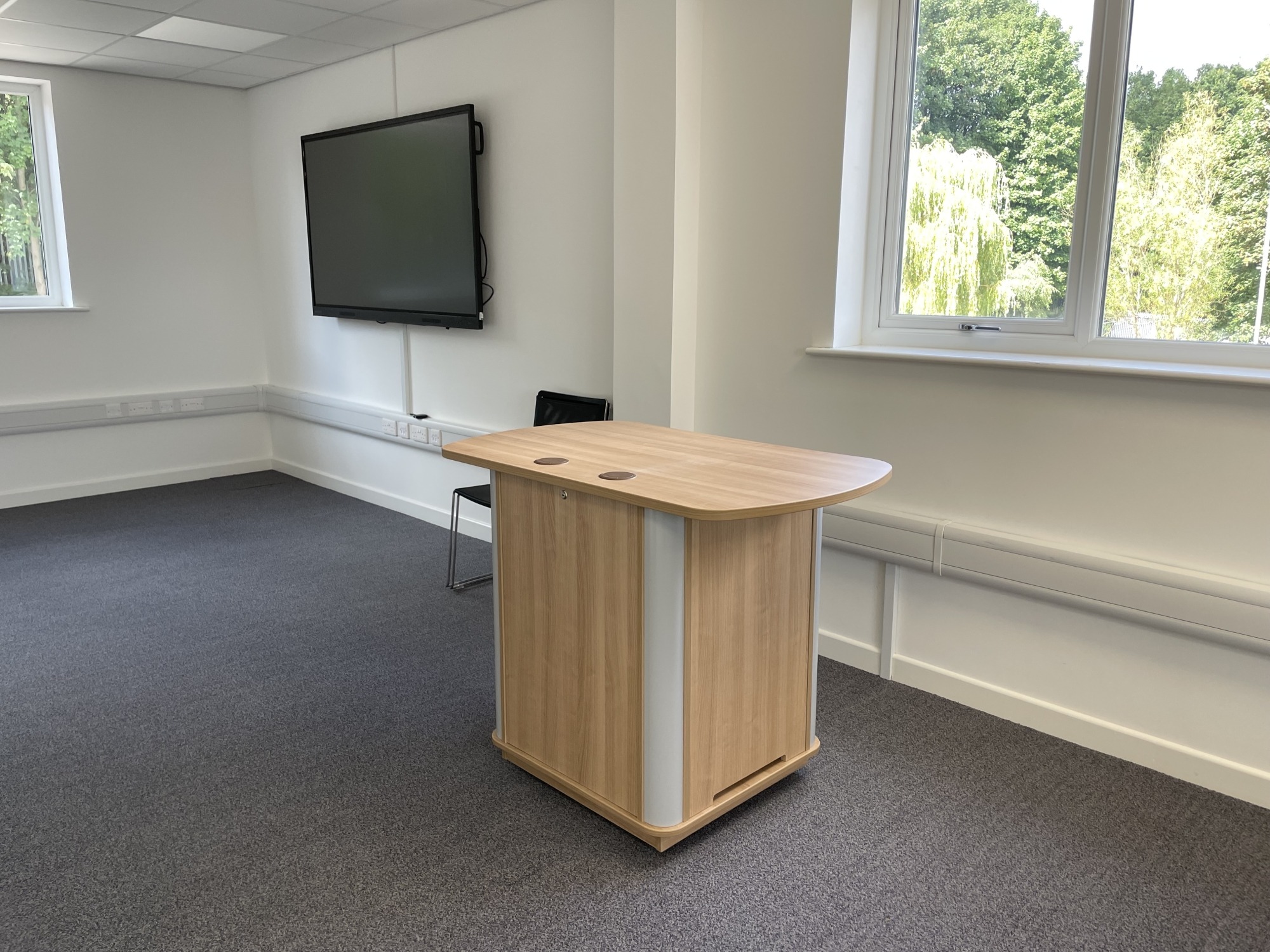
Sosa Executive Chairs:
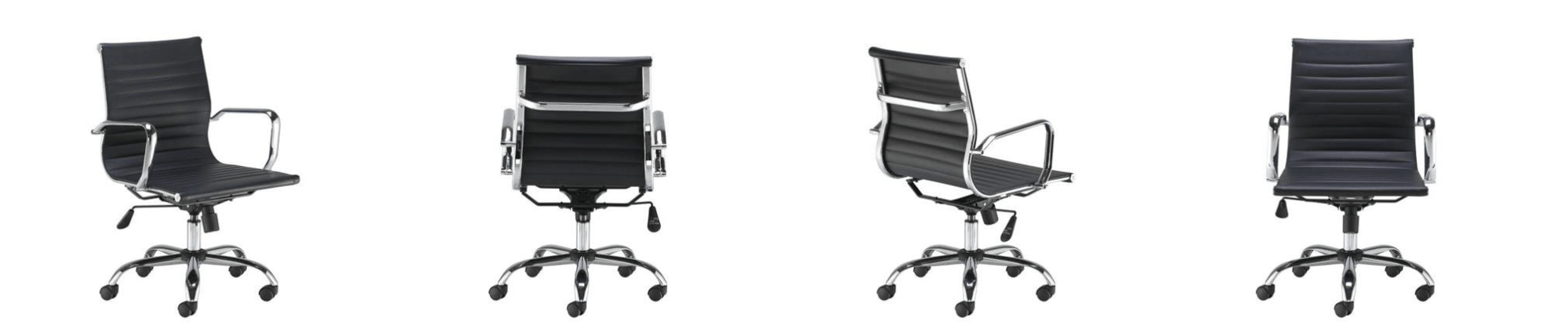
Partners
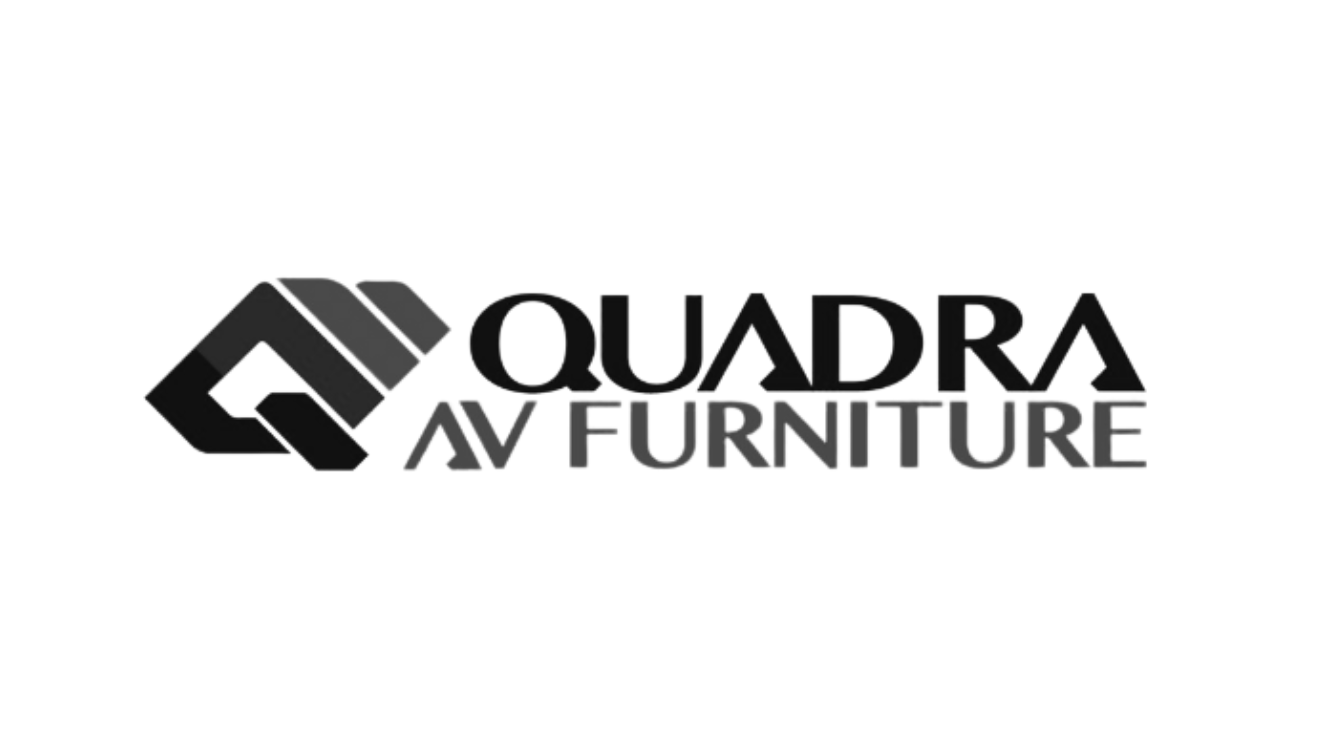
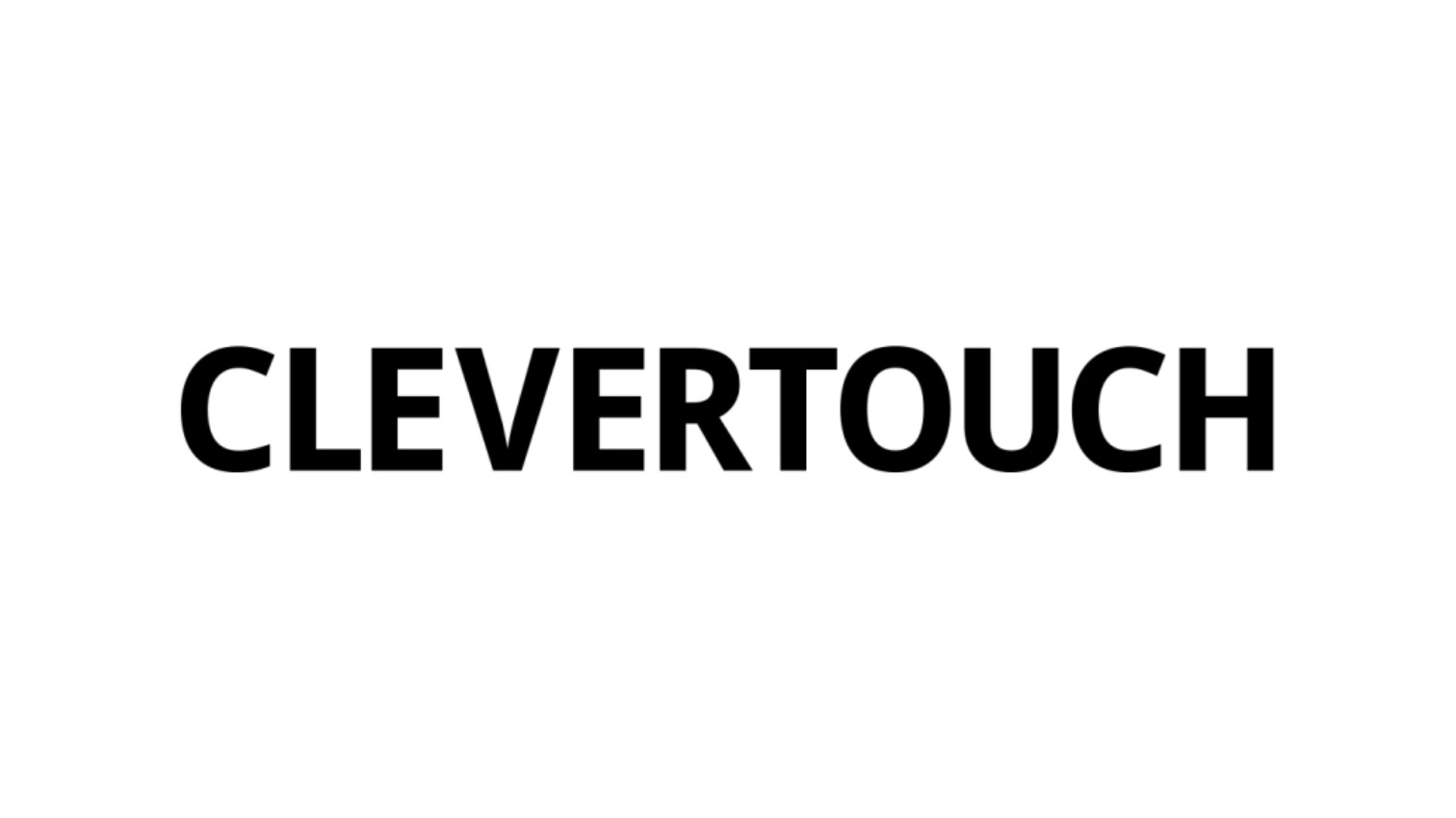
Phase 2: AV Installation
The final part of the jigsaw was the audio visual components which were installed by Roche engineers. Clevertouch was chosen as the key brand so varying sizes of IMPACT Plus touchscreens along with CleverShare dongles and CleverCams were incorporated alongside the likes of DisplayNote, Kramer and Jabra.
The Meeting Room - 7-Seater Alliance Collaboration Table incorporating a Clevertouch IMPACT Plus 55" Touchscreen:
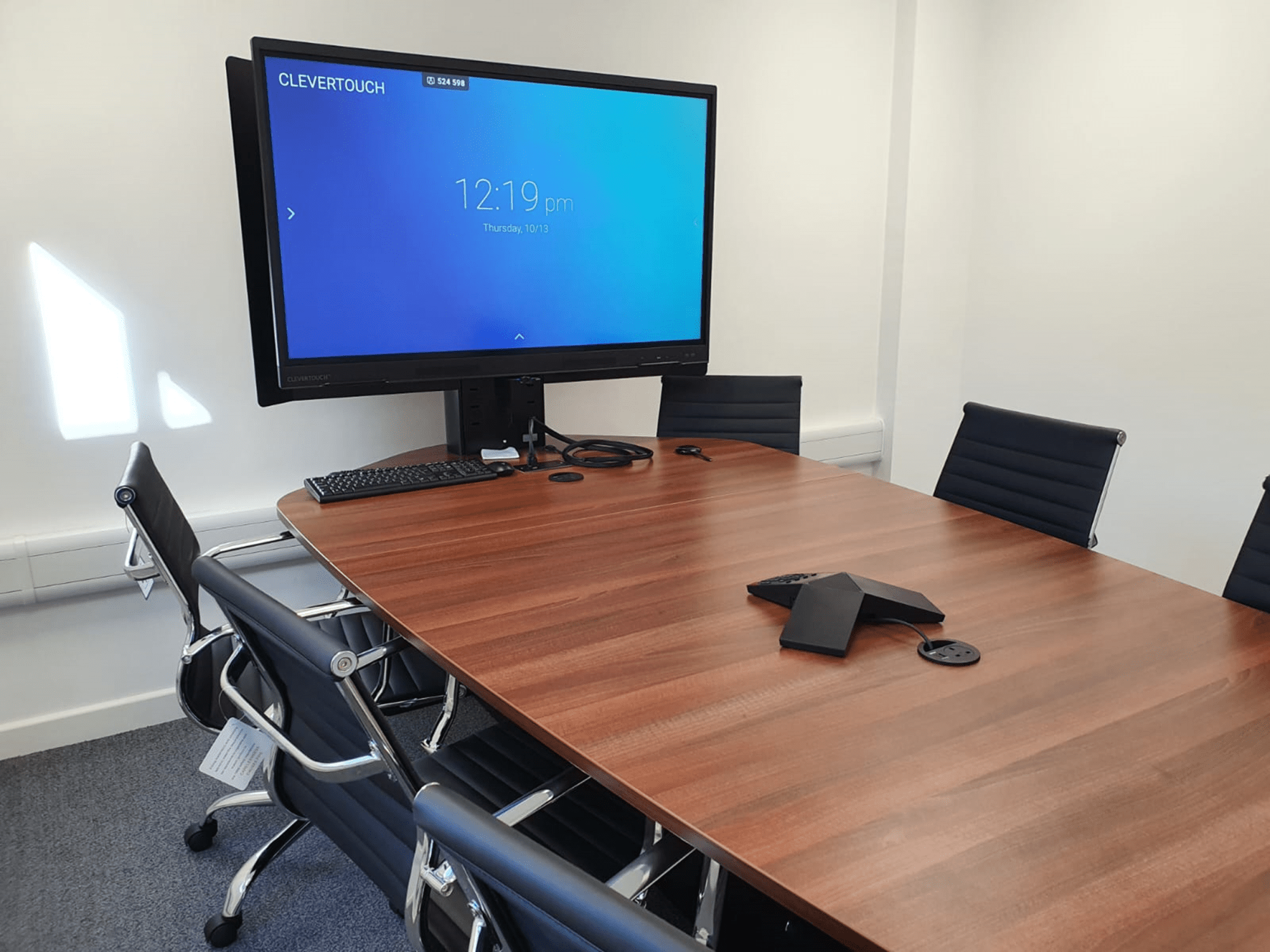
The Main Boardroom - 20-Seater Boardroom Table alongside a Clevertouch IMPACT Plus 86" Touchscreen:
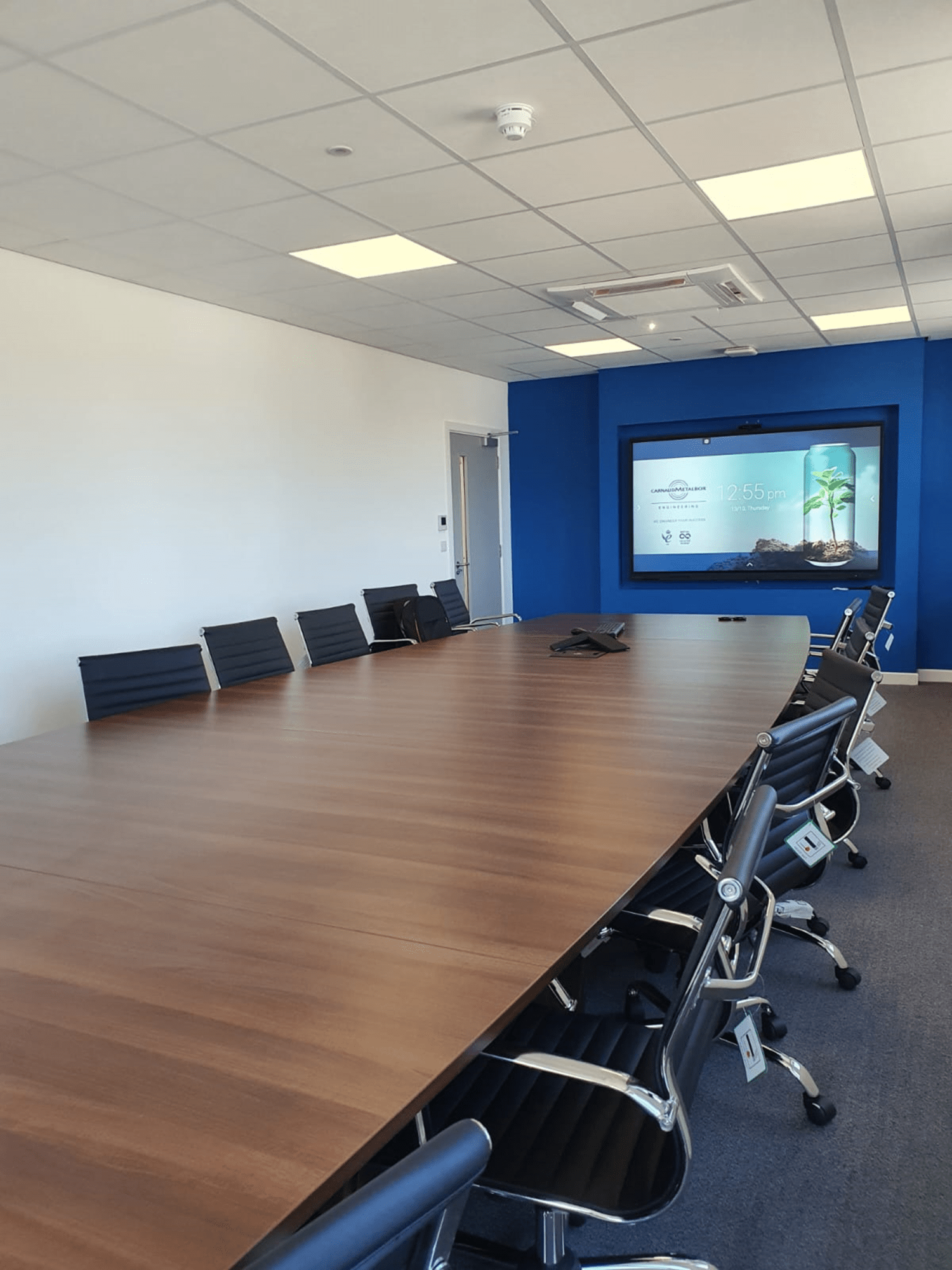
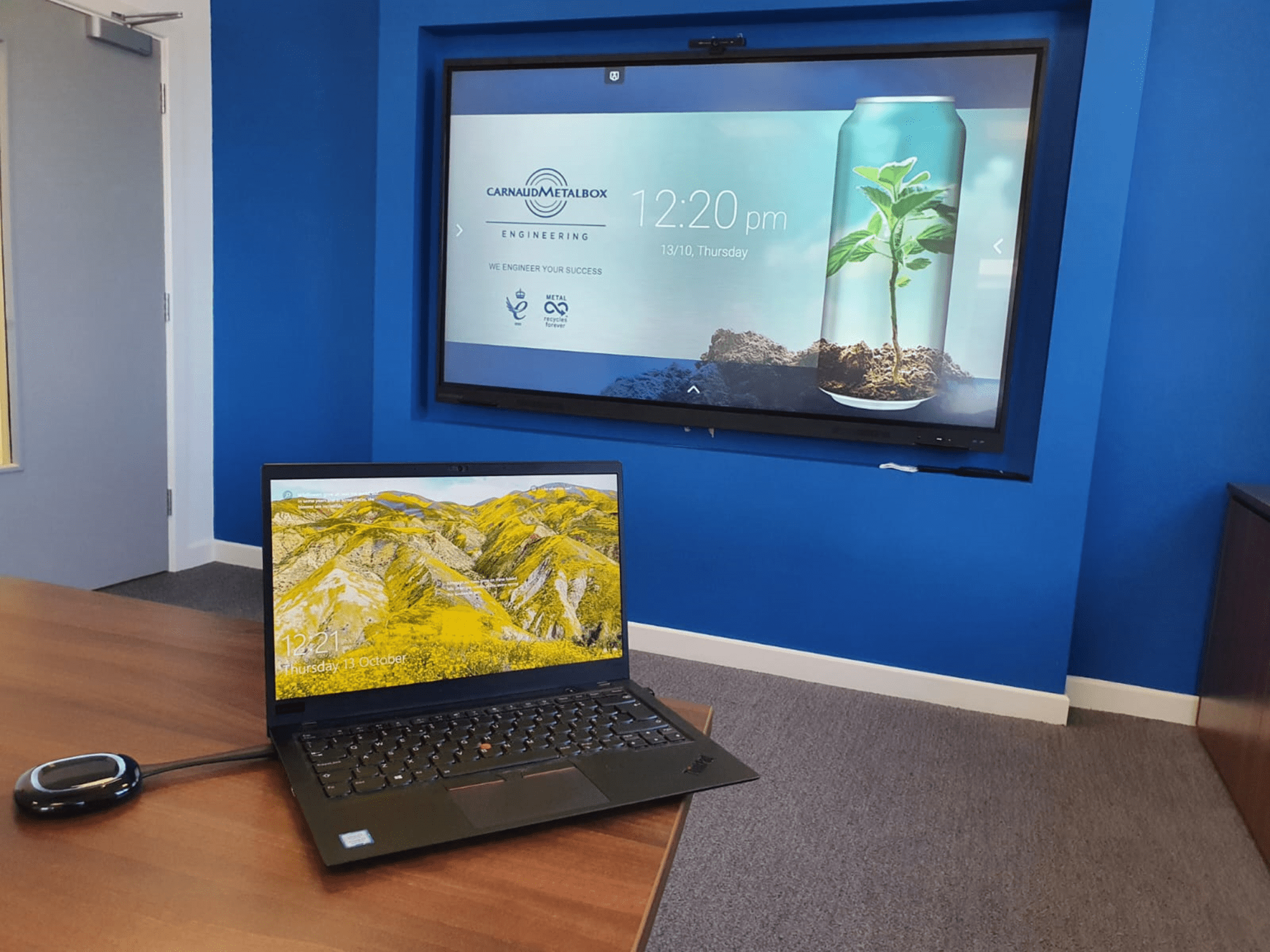
The 2 Vice Principals Offices: 5-Seater Alliance Collaboration Tables incorporating Clevertouch IMPACT Plus 55" Touchscreens:
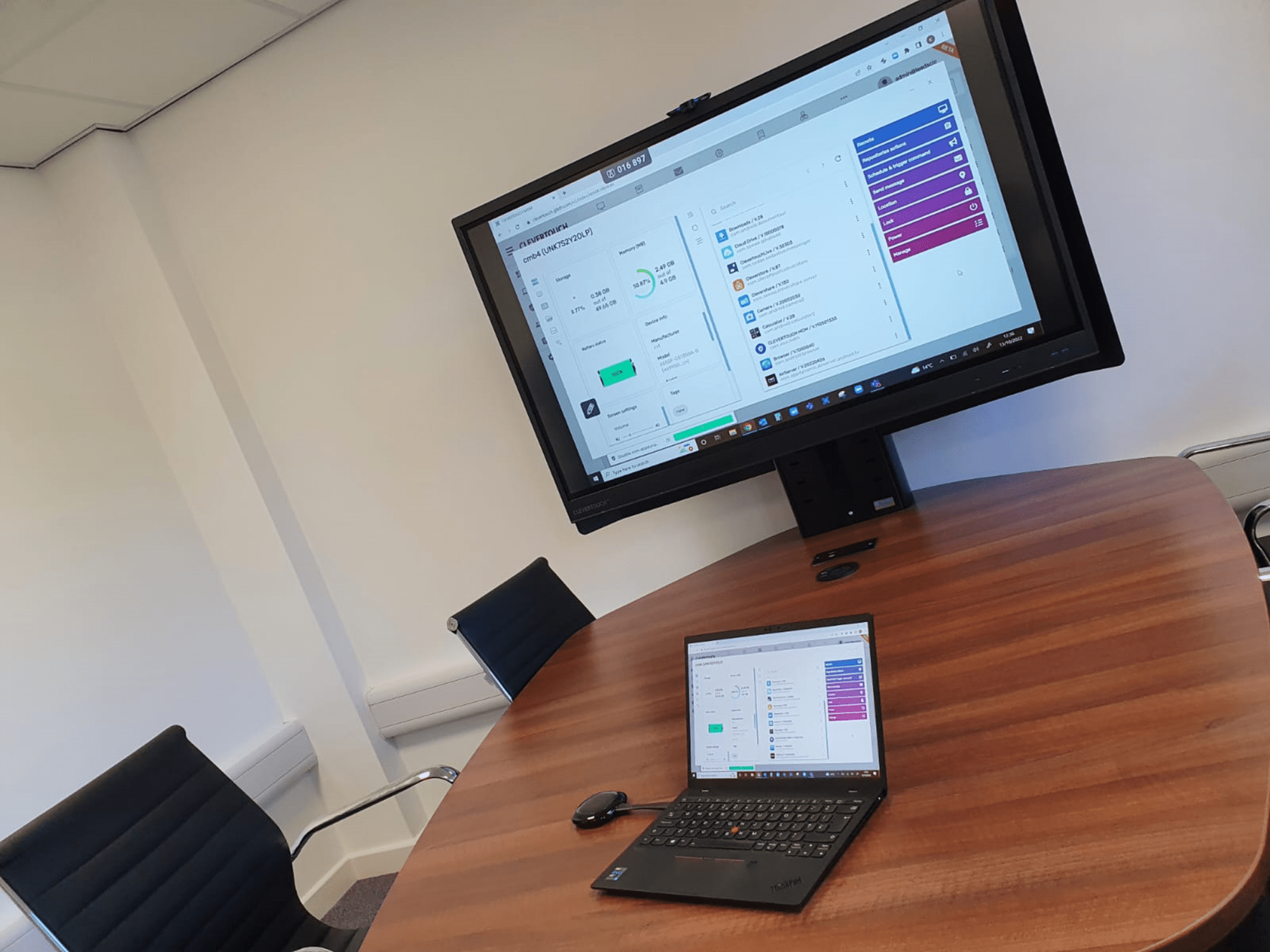
QAVF were able to join us on-site to guarantee the highest possible standard of installation and ensure any tweaks to the original designs were carried out to ensure optimum performance. CMB Engineering now have first class boardroom facilities which are backed up by Quadra's 10 YEAR fair wear and tear warranty.
Feedback
We really enjoyed working with Ben and the rest of the team at Quadra on this project. The furniture looks superb and really makes a statement, especially in the Main Boardroom with the stunning 20-Seater Table. The other units across the site all compliment each other and look extremely professional. We are looking forward to working alongside Quadra on future projects. - Stafford Lund, Sales Manager - Roche AV
"We were contacted by Stafford Lund of Roche AV to see if we could help with a large furniture fit out for one of their clients, we arranged a site visit to talk to the end user to discuss what furniture they needed and to look at the spaces. While there we were able to roughly measure the rooms as it was still a building site so we could start drawing the floor plans to work out the available space. We like to check that what ever we manufacture will fit into the rooms and still allow people to moved freely. During the design process we re-visited site once again when the rooms were near completion to double check dimensions. We then worked up the final drawings and shared them with Roche AV for sign off and so they could check what we had designed would work for them and their AV install. Following sign off on the designs and orders placed the job went live with our production team.
For a large project it was straight forward due to Roche AV and their customer knowing what they wanted, it was great to work with the team at Roche and J-LEC on this project. The main thing is to always keep talking with all parties and Roche certainly did this which helps everyone know where we are on the project at any one time. We look forward to partnering with Team Roche again on more projects". - Ben Crooks, Operations Director - Quadra AV Furniture
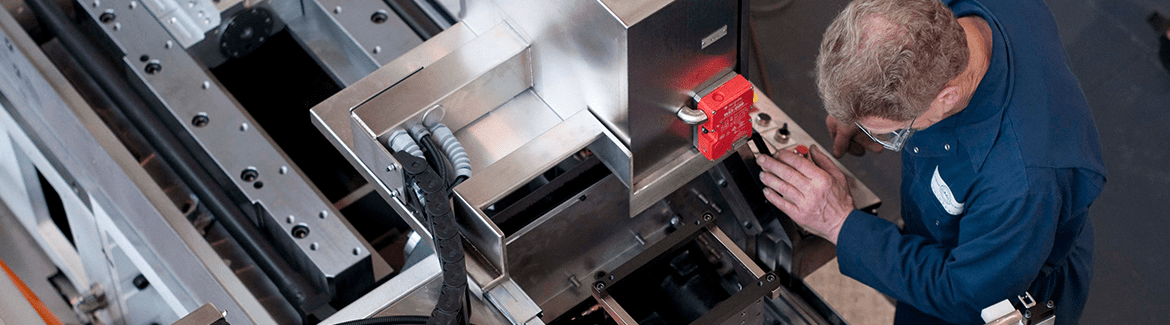